Corporate Vending Solutions, Remote Monitoring, Inventory Control & Management Tools & MicroMarket™ Retailing Solutions
Our innovative corporate vending solutions offer you cost effective options whether it means retailing drink, snack and food items or dispensing of consumable goods such as PPE or safety articles, first-aid items, toiletries goods, stationary articles, bar / liquor products, tools, or spare parts, across a myriad of sectors including Education, Hotel & Bar, Mining, Oil & Gas, Corporate, Public & Private Sectors, OH&S (Safety Station), Hospitality, Food & Beverage.
Vendpro offers you cost effective corporate vending solutions to your inventory and compliance management challenges. You get improved real time monitoring capability with our remote monitoring vending system, which allows better control and easier compliance whether your aim is to reduce costs, manage usage of consumable goods or to achieve Occupational Health and Safety (OH&S) objectives.
We provide a range of cashless payment inventory control / management solutions to suit every need and budget. Examples of these include:
- Stand-alone no traceability of usage such as when vending in the catering and hospitality environment.
- Integrated to a variety of facilities management systems secure, full issue customisable report / traceability of consumable products issued e.g., controlled issuing of PPE in safety station vending machines, stationary, bar / liquor etc.
- Self-checkout secure micro market vending and retailing opportunities e.g., advanced vending functionality in corporate crib / break / lunchroom applications etc. Australia’s licensed provider of 365 Micro Market solutions.
TCN PPE Vending Machines
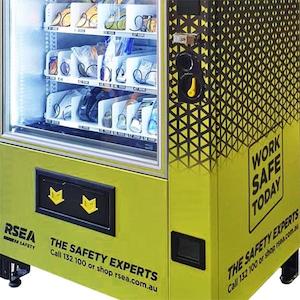
TCN is the world’s second largest vending machine manufacturer. Exporting machines to more than 100 countries in America, Europe & Asia, it has one of the biggest vending machine factories in China covering more than 100,000 square meters.
TCN supply quality vending machines and solutions that offer advanced embedded electronics utilising VisualVend technologies. TCN vending machines’ advanced vending motor capabilities support coil and conveyor belt as well as lifter dispensing options. TCN Australia’s PPE unattended corporate vending solutions include PPE & industrial vending machines complemented by integrated smart pickup and return locker box systems.
The TCN Difference
TCN vending machines can be customised to vend almost any PPE/industrial item to meet the specific nature and requirements of most industrial sites. TCN locker boxes allow storage and issuing of a range of larger and expensive industrial equipment such as hard hats, industrial drills, and associated equipment; even boxes of widgets where a user’s usage can be limited to a maximum number of widgets.
TCN Vending Australia, in collaboration with several global vending manufacturers, developed VisualVend@Safety™, after conducting extensive research and development in the vending and unattended retail markets in Australia and abroad
VisualVend@Safety™ is the world’s first purposely built Vend2End Asset Tracking Software platform specifically designed in Australia for the personal protective equipment (PPE) & industrial sectors for vending in unattended environments. The VisualVend software tool (a platform designed for unattended vending requiring a vending machine to operate), was developed by Enabled 2 GO Technologies – a cc2GO Group Company – specifically for the vending industry. The Group has been in vending telemetry, payments, wearables, and mobile/telecom communications for almost 20 years.
This proven solution has helped address industrial and safety equipment supply in unattended locations and has positioned TCN Vending Australia as one of the fastest growing PPE vending solution providers in Australia and New Zealand.
Frequently Asked Questions – PPE Vending Machines
What PPE products can I vend?
We can manage the vending of most PPE/industrial and chemical products including, but not limited to:

Can I use my current stockist or stock my own products?
You can use both methods. That means you can retain the independence to competitively bid the supply of your PPE and other consumables and/or work with your suppliers to keep your costs down.
What savings can I expect?
A saving of at least 10-45% (and even up to 60% on some items) on your material usage is to be expected. Significant savings in labour transpires from less time spent at waiting for service at the stores counter, the need to fill out and approve supply demands etc. In addition, accurate and real-time information and traceability on product use saves a significant amount of management and reporting time whilst increasing compliance to regulatory requirements.
Are there any limitations on the product items I can dispense?
No, you have the freedom to stock and vend almost any product you choose with the experience and support of Vendpro, such as PPE, industrial items, or consumables including drill bits, stationery items, adhesives, batteries, sunscreens, spanners, or other products. The only limitation is the physical size and weight of an item, but our flexible machine set-ups can accommodate a range of different pieces.
Can we restrict access to certain items or limit the quantities an individual can have?
Yes, VisualVend@Safety™ includes the support of groups and individual employee/user access to items and can include number of products accessed limitations.
This can be done with the customisable back-end cloud portal that allows you to create different user groups (e.g., supervisors vs. general staff) and then restrict access to certain types of products for that group. In this way you help ensure staff are using the right gear for the right task and limiting excess usage.
Can we use our existing employee access cards to use the machines?
Depending on the type of cards being utilised and the current security arrangements in place, there are several options which are supported. We support a range of RF, NFC and PIN based input cards and FOBs.
Any systems integration is possible and will require the assistance of the IT department within the organisation as well as the security card providers. They can also support staff ID and/or PIN input for any existing employee cards. Alternatively, we can issue you with a generic key tag and/or fob.
Who is responsible for filling the machines and how hard is it?
There is an option of using your staff, your suppliers, or another third-party provider. It is not difficult to refill a machine and care needs to be taken to ensure trouble-free dispensing. Refill varies but can take about 15 to 45 minutes to completely fill a machine depending on the product. TCN Vending machines have a simple pull-out tray to improve efficiency in refilling items.
Where do the PPE machines have to go?
PPE machines can be stored in indoor and outdoor environments and in various extreme weather conditions. Placing PPE machines where they are easily accessible is ideal to maximise efficiency of movement e.g., start of shift areas, plant access points, workshops etc.
Is special packaging required for the products?
Most items can be vended without any special packaging. That’s because we can tailor each aisle “slot” with the right set-up to match the products and ensure trouble free operation. We include extensive aisle slot testing and provide expert training as part of the Vendpro service and can advise you on suitability and limitations on an individual product basis.
PPE Vending Machines
PPE Vending Machines are designed to dispense a wide range of personal protective equipment and safety supplies to staff and contractors alike. These machines can be setup wherever there is space and a need for personal hygiene products.
The PPE Vending Machine management system can issue emails or text message status warnings for events such as ‘machine empty’, ‘no sales within a defined period’, ‘selections empty’, ‘machine offline’ and more.
These machines are smart machines meaning they are cashless, utilising an allocated FOB or card to access the items. Purchase details are then saved against that specific employee or contractor’s card for ease of cost allocation. See full range here.
Restocking is done by the staff or contractors onsite as and when required. A stock report is generated using the online web-based system advising of the ‘real-time’ stock levels and what items need replenishing. This same system manages the administration, inventory, card holders, vending history, cost allocation, daily sales, daily product sales, usage invoice and all other reporting. These can either be viewed on-screen or exported from the system in PDF or CSV file format. Report breakdown includes:
Product list: A categorised list of all the products up-loaded on the system. Customer product numbers corresponding with the customer’s current inventory control system are allowed.
User card holder report: Each FOB holder can be limited to a pre-set daily and/ or total spend. Also, FOBs can be assigned to different user types e.g., staff, contractors or visitors. This allows generation of user reports by FOB type and/or by FOB assigned to different user departments/cost codes.
Vend history report: A report showing every transaction made during a defined period. For example, reporting includes details on the machine, card holder, product description, units taken (one item per vend), the transaction amount and date and time of transaction. Reporting is totalled for units and dollar value dispensed. Reports can be exported in CSV-format and manipulated by means of excel pivot tables etc. to total sales by FOB holder etc. Reports can be auto emailed to customer representatives on a pre-determined frequency e.g., weekly, monthly, quarterly, or annually.
Cost allocation report: A report tracking the job number that an item has been expensed to (used for customers who want to share the cost of the item with their end-user).
Daily sales report: A report showing the total units dispensed and their dollar value by days for a specified period.
Daily product sales report: A report showing daily sales / vends by product for all products in the machine.
Re-stock report: A report showing the number of products required to re-fill the machine at the time the report is created.
Sales report: A report summarising by product and dollars of everything sold / dispensed from the machine for a specified period.
Weekly invoice for usage by user / employee: A Report showing the total spent on each FOB for the week. It also reports a balance of the total “credit” on all the FOBS both individually and combined.
There are many benefits to having a PPE Vending Machine on site and some of these benefits include: personalising the items stocked, it’s fully automated and secure, no stock on hand to worry about, zero wastage and always being on-top of stock availability. It’s a machine almost every work site needs.